

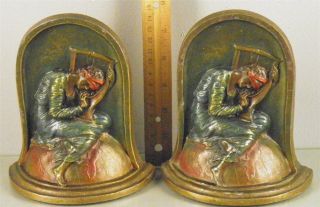
#Iron bookends drivers#
If the British Ironwork Centre is not notified to damage within 48 hours, the British Ironwork Centre is not able to claim to either the manufacturer or the courier.įor larger deliveries, including pallets, you agree to check the goods for damage or fault, before signing the courier drivers delivery note. If any fault is visible, the customer must notify BCMW within 48 hours of delivery. The vast majority of bronze-clad bookends were made in the Art Deco 1920s.Ī great many figural designs exist: animals birds nature and marine life, men women couples and children, Arabian Asian Egyptian and Native Americans, architectural themes, canines felines dogs and cats, mythological characters, notable presidents, patriotic military ships nautical and maritime, literary greats, and much more.For small deliveries which arrive with couriers, the customer agrees to open all boxes and thoroughly check the goods for damage or faults. Very popular in the bookends’ world from about 1905 to 1935, only a single manufacturer survived beyond WWII. Notable to this process was the time and skill involved - the time spent in the electroforming bath could be several days, with significant levels of electrical current needed to achieve the bronze skin. They are essentially a plaster sculpture encapsulated in bronze. Unlike modern industrial-part electroforming where the form (or mandrel) is then removed, these bookends still have their plaster core.
#Iron bookends skin#
Electroformed differs from electroplated in that the skin is much thicker, on average perhaps several-to-a-dozen times the thickness of heavyweight aluminum foil. Electrical current was passed through the electrode and the plating bath, and a bronze “skin” formed around the plaster core. Similar to electroplating, this plaster-cast form was then suspended in the fluid of a plating tank. Various companies had somewhat different methods and patents, but, generally, this initial plaster casting was coated with a material to make it more electrically conductive - and there was an electrode-wire within before the plaster was cast (the end of which is often still visible within a dimple on the bottom). The most complex manufacturing process of the various types of antique bookends, bronze-clad bookends begin as a plaster casting.

We think “bronze-clad” is by far the best label for this type of bookend, but folks also refer to them as “plaster-filled bronze”, “electroformed bronze”, “weighted bronze”, “bronze coated”, “armor bronze” and “galvano bronze” (lowercase a-or-g, to differentiate from the companies with the same name). Much less brittle than iron, bronze melts at a relatively high temperature. Other elements are also sometimes used in bronze alloys - be it phosphorus, manganese, aluminium, or silicon - hence the many different “bronzes” that exist. Spelter is still used today to make cheaper cast metal products.īronze is an alloy consisting mostly of copper, usually with tin as the main additive (another copper alloy, brass, is copper alloyed with zinc). Spelter bookends from the Art Deco era were most often made by permanent mold slush casting (which means they are hollow). Because this alloy has a much lower melting temperature than bronze, it was commonly used to make less expensive products (not just bookends, but all sorts of household items). Spelter generally refers to an alloy of zinc and lead, and is often referred to as gray metal, white metal, pot metal, and others. Often sand cast, they may have a bronze “wash” or other plating, but if a magnet sticks they contain ferrous material, and are therefore generally considered to be iron (except for the occasional steel railroad-rail cutoff).
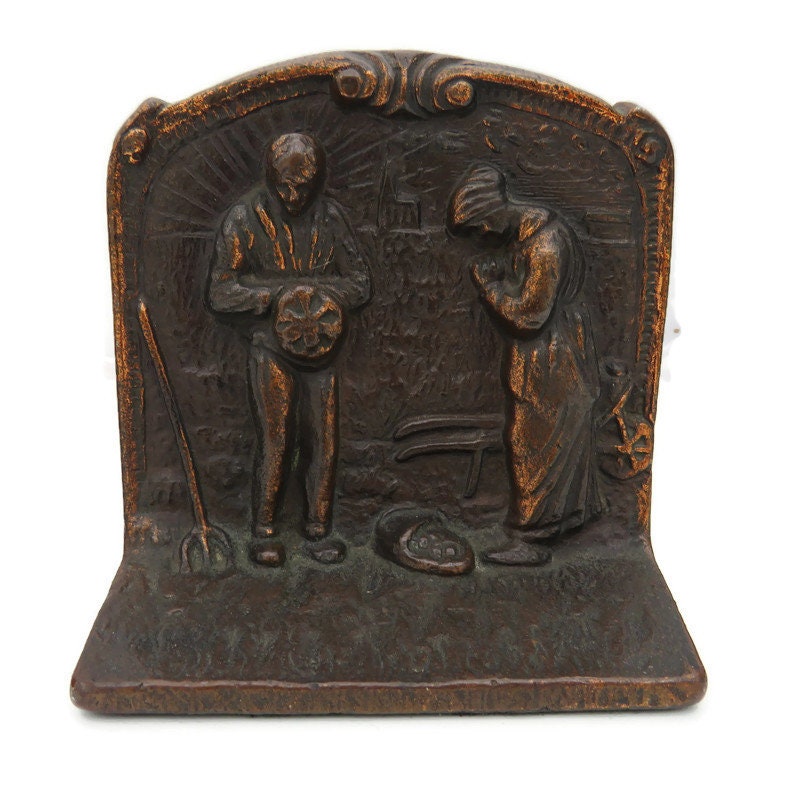
Rounding out the historical record are one very famous “Bookends” produced in vinyl, if you count the album & title track released by Simon & Garfunkel in 1968.Ĭast iron are among the easiest to identify an ordinary ’fridge magnet sticks to them. Most collectible vintage or antique bookends fall into one of four categories: iron, spelter, solid bronze, and bronze-clad - other pairs were produced in alabaster, marble, onyx, gypsum, glass, pottery, and hardwood.
